Key facts on air-to-air energy recovery
Air handling units are usually equipped with heat exchangers. The purpose of a heat exchanger is, despite its name, to make use of the heat or cold contained in the extract air. The efficiency of a heat exchanger can be described in terms of temperature efficiency, i.e.in terms of how much of the energy (heat or cold) is transferred from the extract air to the supply air. The challenge is to achieve the highest possible efficiency with the lowest possible pressure drop. Read more about the most common types of heat exchangers in this guide.
Rotary heat exchangers
A rotary heat exchanger consists of a rotating wheel with a multitude of small ducts made of aluminium. The warm extract air heats the ducts which transfers heat to the colder supply air. The temperature efficiency of balanced supply and exhaust air is high. Normally, frost never forms inside a rotary heat exchanger. This allows high annual energy efficiency to be achieved.
The rotary heat exchanger also effectively recovers cooling energy while moisture is recovered with a sorption-treated rotor. Normally used in commercial buildings such as offices, schools, etc.
Read more
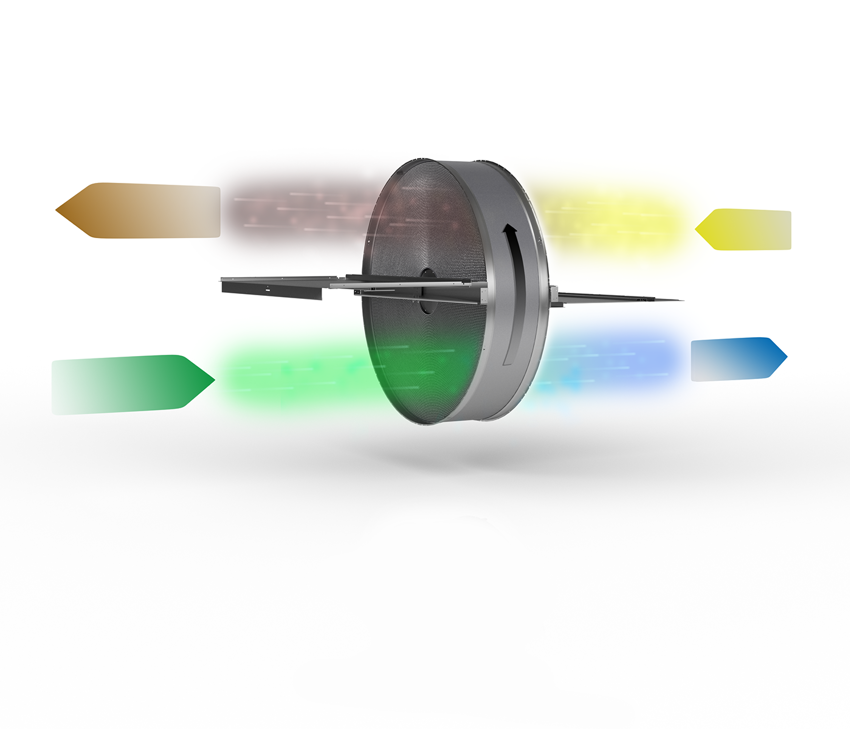
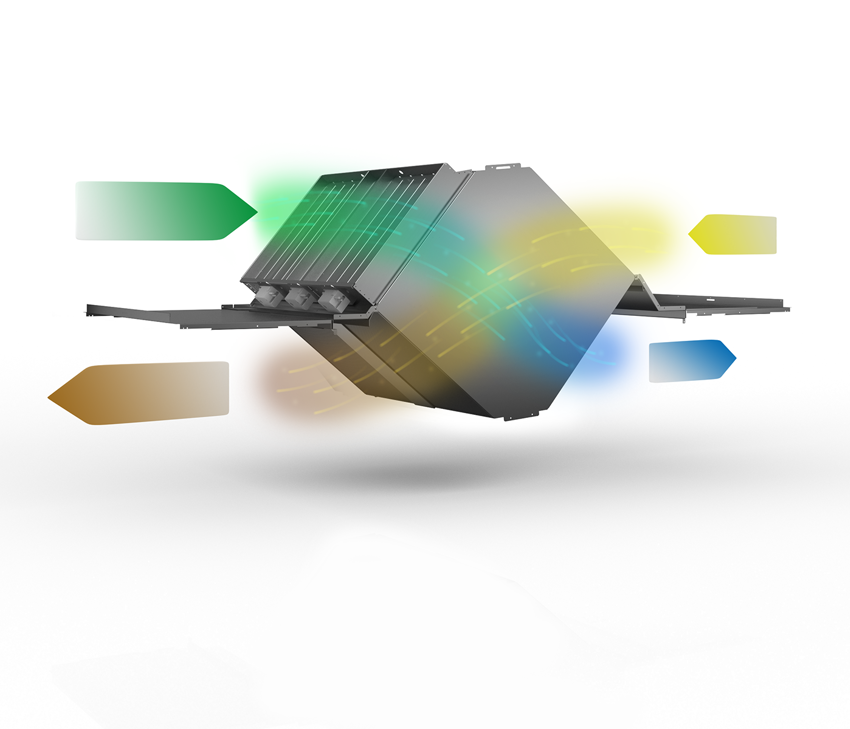
Plate heat exchangers
A counterflow plate heat exchanger consists of thin aluminium fins - plates - that form air ducts where the extract air counterflows the supply air for the best temperature efficiency. The warmer extract air heats the plates which transfers the heat to the colder supply air. The supply air and extract air flow in completely separate ducts, meaning that any odours or particles in the extract air are normally not transferred to the supply air.
The temperature efficiency of balanced supply and extract air can be as high as the rotary heat exchanger, but with the disadvantage that defrosting has to be dealt with.
Usually used in homes or facilities where there is a risk of odour transfer.
Read more
Coil heat exchangers
A coil heat exchanger has one liquid coil in the supply air and one in the exhaust air. A heat carrier is pumped around a circuit between the coils, the air heats the liquid in the extract air coil and the liquid heats the air in the supply air coil.
The temperature efficiency of balanced supply and exhaust air is slightly lower in comparison to rotary or counterflow heat exchangers.
Ideally used when completely separate air flows are required, normally in hospital environments, but also for recycling process air in industrial environments.
Read more
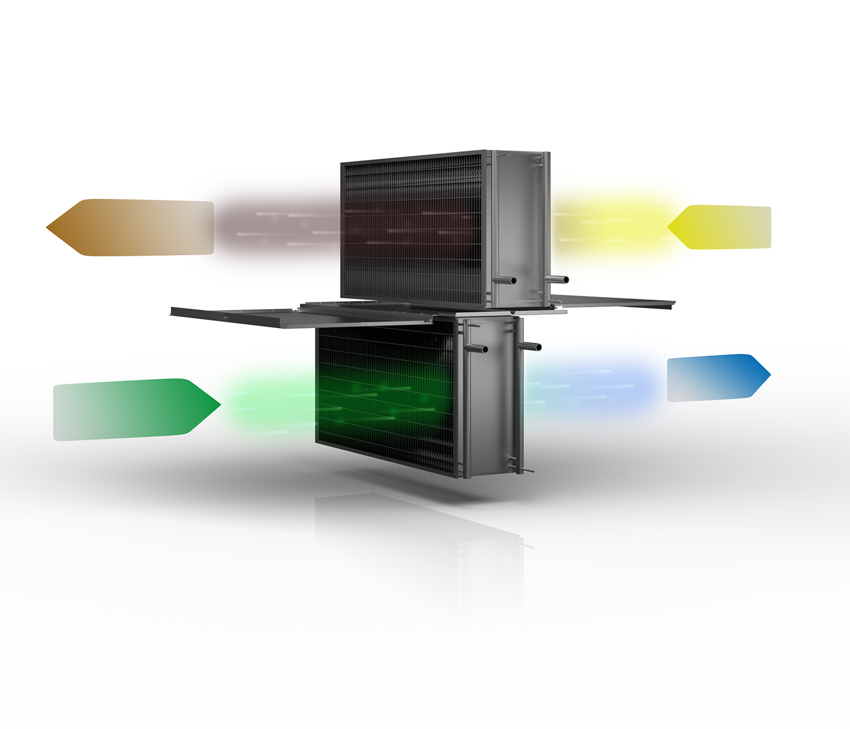