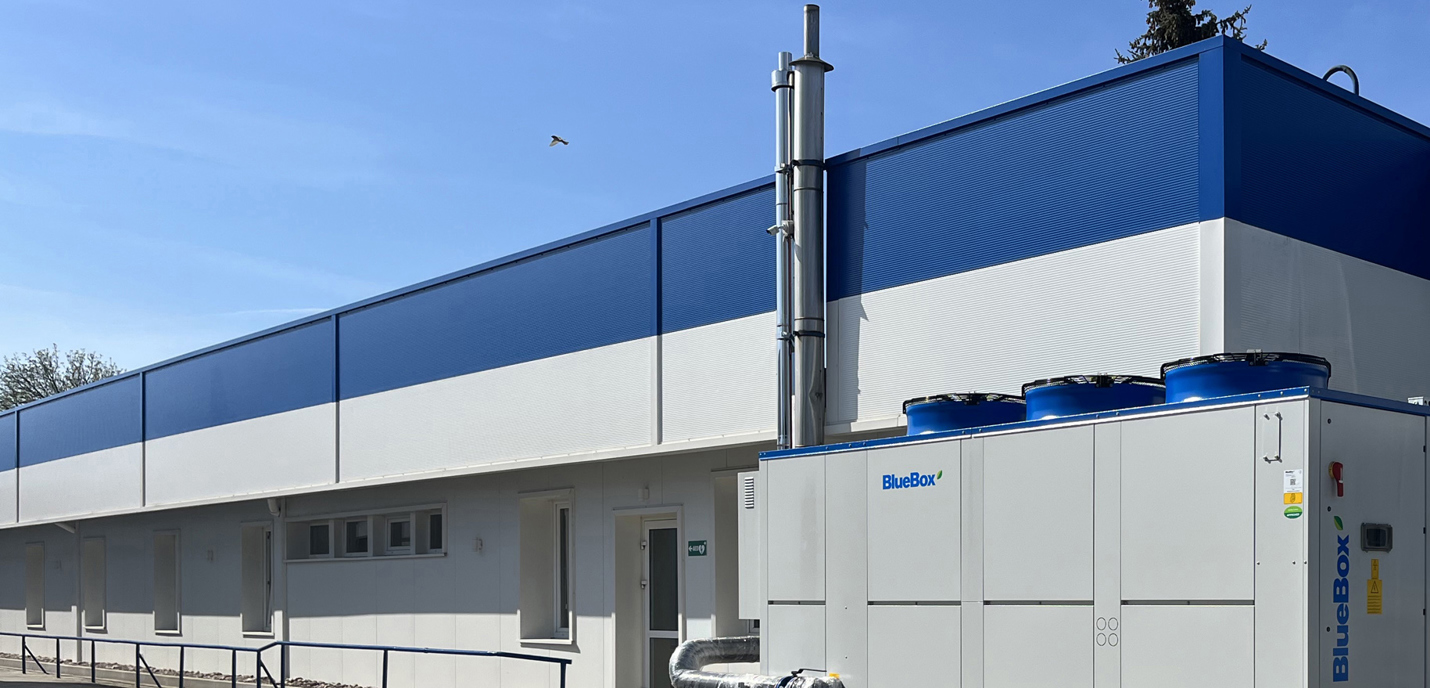
A challenge met in two steps
This is ITC Metal
ITC METAL, located in Skarszewy in Poland, was established in 1989. It is a modern and well respected export company in the metal industry, specialising in wire products, pipes and steel sheets. The company’s business idea starts with careful design of steel products, specified and requested by the customer, it continues with a detailed manufacturing processes and ends with delivery of the final tailor made product.
One project, two steps
The ITC Metal production plant was in need of a modern solution for ventilation, heating and air conditioning (HVAC) and Swegon was assigned to provide a variety of products. However, the two main objectives were to reduce the operating cost for ensuring a good indoor climate in the premises and to reduce the need for heating from the existing boiler, running on natural gas. We were able to share our expertise and we turned out to make deliveries in two stages.
The first delivery included air handling units and a multifunctional unit with a 4-pipe system, where the latter enables simultaneous production of heat and cold. The second stage included three additional heat pumps with a somewhat modified operation mode to answer to the requirement of energy efficiency.

The initial step
Let us describe the first phase of the delivery. The air handling units of model SILVER M were supplied to the galvanising hall. At this stage of the manufacturing procedure at ITC, the need for fresh air varies depending on the technological processes occurring at the time. The air flows can therefore vary between 25-100%.
Due to the characteristics of the industrial activities, the air handling units have been delivered without heat exchangers, normally highly recommended from an energy utilisation perspective. That in turn, explains the need for external units for heating the supply air. We delivered heat pumps of model ZETA Rev and TETRIS W Rev, both from our BlueBox range. However, the technological process also has a clear demand for cooling all year round.
Get familiar with our airsourced heat pumps
A holistic approach to find a suitable solution
With the above said, we took a holistic approach and looked at the energy balance of the entire solution. It was decided, in addition to the AHU and heat pumps, to also provide the solution with a multifunctional unit which operates with a 4-pipe system and enables simultaneous production of heat and cold energy. An OMICRON unit, also from our BlueBox range, was specified.
The unit was connected to the pre-heater of the air handling unit, which allows for heat recovery by utilising the hot air from the cooling process of the solution. When in place, there was a remaining need to heat the air for the premises, which is why heat energy from the boiler room was decided to be used. When a solution is set up this way, it allows for good flexibility since the OMICRON unit will work as a heat pump as long as there is no cooling need.
Taking on the second step
Vast variation in temperature
In this stage, it was necessary to closely analyse the available technical possibilities due to the vast variation of the heating medium, ranging from 50°C to 80°C. In addition, heat receivers were located in different places of the premises. To ensure that the requirements of the individual heating circuits were met, it was decided to use two air sourced heat pumps with a wide operating range. These made it possible to obtain heating of 53°C and 58°C.
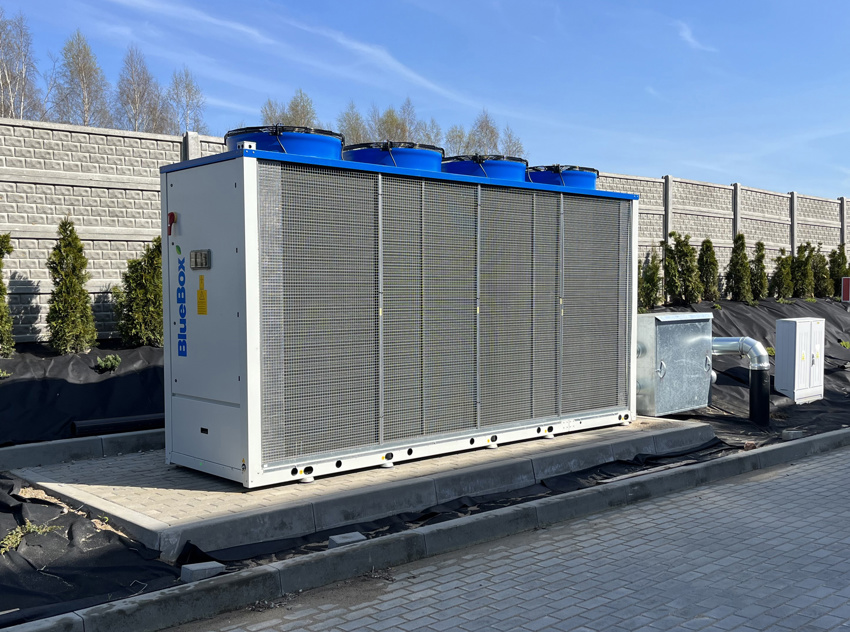
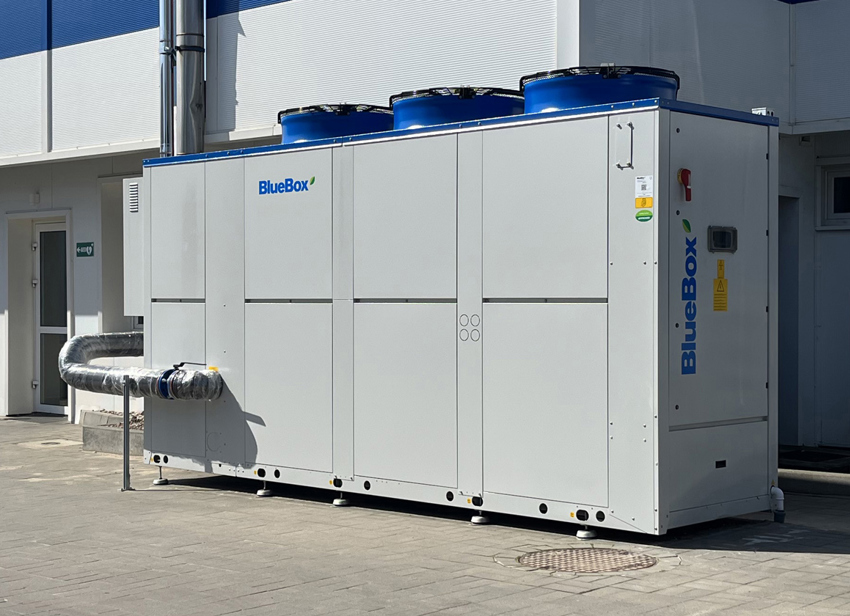
High temperature water from multifunctional unit
To maximise the efficiency of the heat recovery system, we proposed an alteration of the air handling units. The initial assumption was that the multifunctional unit produces heat only during the colder period of the year, from October to mid-April. For the rest of the year it was planned to operate the unit only in cooling mode, which mean that all the heat generated from the cooling process of the industry was to be removed to the outdoors since it only held a temperature of about 45°C, less than required. It was then evaluated if the warm water flow from the OMICRON unit was possible to be altered, in order to be used as an energy source for a water/water heat pump. It turned out that the heat pump could guarantee a temperature of 80°C, despite the fairly low water temperature (45 degrees Celsius). Said and done, TETRIS W Rev units were selected for the project.
The final result at ITC Metal
Thanks to the analysis above, the supply air for the air handling unit, coming from the multifunctional unit, was directed to the water/water heat pump when the supply air had less heat demand. The automation system for the entire solution was also modified in order to make it possible to manage the operation of the AHU and the heat sources simultaneously. The result is a complete installation which operates all year round, with full heat recovery and a minimised utilization of the heat from the boiler room.
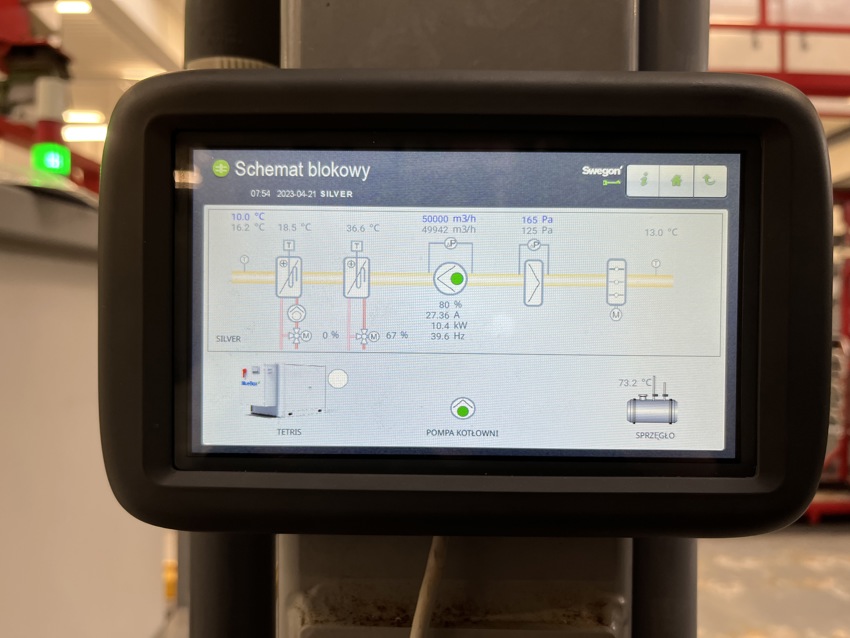
Products
Here are some of the products provided in this project